Comprehensive Overview: What is Porosity in Welding and Just How to stop It
Comprehensive Overview: What is Porosity in Welding and Just How to stop It
Blog Article
Porosity in Welding: Identifying Common Issues and Implementing Finest Practices for Prevention
Porosity in welding is a pervasive issue that frequently goes undetected until it creates significant issues with the honesty of welds. In this discussion, we will discover the vital aspects adding to porosity formation, analyze its detrimental results on weld efficiency, and review the ideal methods that can be embraced to minimize porosity incident in welding procedures.
Usual Reasons For Porosity
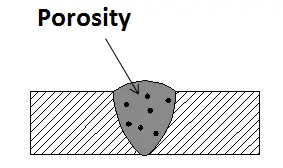
Making use of filthy or damp filler materials can present impurities right into the weld, adding to porosity concerns. To minimize these usual reasons of porosity, complete cleaning of base metals, appropriate securing gas selection, and adherence to ideal welding criteria are essential practices in accomplishing high-grade, porosity-free welds.
Effect of Porosity on Weld Top Quality

The presence of porosity in welding can considerably jeopardize the architectural integrity and mechanical homes of bonded joints. Porosity develops spaces within the weld steel, deteriorating its overall strength and load-bearing ability.
Welds with high porosity levels often tend to exhibit reduced impact toughness and lowered capability to deform plastically prior to fracturing. Porosity can hinder the weld's ability to properly transfer pressures, leading to early weld failing and possible safety hazards in essential structures.
Ideal Practices for Porosity Prevention
To improve the architectural stability and quality of bonded joints, what certain measures can be applied to reduce the event of porosity during the welding procedure? Utilizing the proper welding technique for the particular material being welded, such as changing the welding angle and gun setting, can further avoid porosity. Routine assessment of welds and prompt removal of any kind of concerns recognized throughout the welding procedure are essential techniques to avoid porosity and create top quality welds.
Value of Proper Welding Methods
Applying appropriate welding techniques is extremely important in making certain the structural honesty and high quality of bonded joints, developing upon the structure of efficient porosity avoidance steps. Too much warm can lead to increased porosity due to the entrapment of gases in the weld swimming pool. Additionally, utilizing the suitable welding criteria, such Recommended Reading as voltage, present, and travel speed, is important for accomplishing audio welds with minimal porosity.
Additionally, the choice of welding process, whether it be MIG, TIG, or stick welding, need to align with the details requirements of the job to ensure ideal outcomes. Proper cleaning and prep work of the base metal, along with choosing the right filler material, are also essential parts of efficient welding methods. By sticking to these finest practices, welders can decrease the danger of porosity formation and generate premium, structurally sound welds.

Testing and Top Quality Control Actions
Evaluating treatments are vital to detect and avoid great post to read porosity in welding, ensuring the stamina and toughness of the last product. Non-destructive testing approaches such as ultrasonic testing, radiographic testing, and aesthetic examination are typically utilized to recognize potential problems like porosity.
Post-weld inspections, on the other hand, examine the final weld for any type of issues, consisting of porosity, and confirm that it fulfills defined criteria. Implementing an extensive quality control plan that includes comprehensive testing procedures and examinations is vital to decreasing porosity issues and making certain the total top quality of welded joints.
Final Thought
Finally, porosity in welding can be a common issue that affects the high quality of welds. By find this recognizing the usual reasons for porosity and implementing best methods for prevention, such as appropriate welding methods and screening actions, welders can make certain high top quality and dependable welds. It is necessary to prioritize prevention methods to minimize the occurrence of porosity and maintain the integrity of welded frameworks.
Report this page